STAR Eligibility
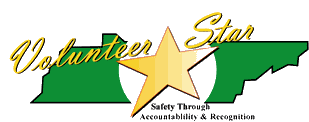
The items listed below will help you determine your eligibility for the VPP. Mentally check each item you currently have or are willing to implement. When you have completed the checklist, go to the SCOREBOX at the bottom of the list to see how your company measured up. Call the VPP Manager in the TOSHA Nashville Office when you are ready to submit your application or have questions.
Rates
Both the average injury and illness rate and the average lost workday injury and illness rate for the most recent three calendar years at the time of approval must be below the most recently published rates for the industry specific Standard Industrial Classification as published by the Bureau of Labor Statistics.
Injury and Illness Rates are calculated (N/EH)x200,000 where:
N = number of recordable injuries and illnesses in one year.
EH = total number of hours worked by all employees in one year.
200,000 = equivalent of 100 full-time workers employees working 40 hour weeks 50 weeks per year.
Lost workday case rates are calculated with the same equation where:
N = number of injuries resulting in lost workdays or restricted work activity.
Management Leadership and Employee Involvement
- A managerial commitment to worker safety and health protection
- Top management's personal involvement
- Safety and health concerns integrated into your overall planning cycle
- Safety and health protection managed in the same way as your productivity and quality are managed
- A written safety and health program appropriate for the size of your site and your industry that addresses all the elements in this checklist
- A results-oriented safety and health policy
- Clearly assigned safety and health responsibilities with documentation of accountability from top management to line supervisors
- Adequate authority given to carry out assigned responsibilities
- Necessary resources to meet responsibilities
- Quality protection for all contract employees equal to that provided for your own employees
- Employee involvement in activities that have a major effect on your safety and health program
- Annual safety and health program evaluations with written narrative reports, recommendations for program changes, action plans, and verification procedures
Worksite Analysis
- A method such as comprehensive safety and industrial hygiene surveys to identify existing or potential hazards in your workplace
- A pre-use analysis procedure for new processes, materials, or equipment to determine potential hazards
- Routine industrial hygiene monitoring of toxic substances and noise
- Monthly self-inspections (weekly for construction) with written documentation and hazard correction tracking
- Routine hazard analysis procedures such as JHAs, JSAs, BJAs, PHAs that result in improved work practices and/or training for employees
- A written hazard reporting system enabling employees to pass on their observations or concerns to management without fear of reprisal
- Accident investigations with written documentation
- Method of documenting all identified hazards until they are controlled or eliminated
- Analysis of trends in injury/illness experience and in hazards found, to identify patterns of problems and to implement program adjustments
Hazard Prevention and Control
- Access to certified safety and health professionals
- Engineering and administrative controls adequate for the hazards at the worksite
- Written safety rules and practices that are understood and followed by all employees
- A consistent disciplinary system applied to all employees (including supervisors and managers) who disregard the rules
- Written rules for use and maintenance of personal protective equipment
- Written plans to cover emergency situations
- Hazard correction tracking procedure
- Onsite or nearby medical and emergency services
- First aid and CPR-trained personnel available onsite during all shifts
- Use of occupational health professionals in hazard analysis as appropriate
- Documented ongoing monitoring and maintenance of workplace equipment
Safety and Health Training
- Manager, supervisor, and employee training with emphasis on safety and health responsibilities
- Training in the use and maintenance of personal protective equipment
- Emergency preparedness drills, including annual evacuations
- Documentation of all training received, including assessment procedures
Review
- Your written safety and health programs and all documentation relating to the programs (see the most recent VPP Federal Register Notice) must be available for OSHA review
Concurrence
- Formal signed statements from any collective bargaining agents indicating support of your application to the VPP
- Where no collective bargaining agent is authorized, employees understand the VPP and raise no serious objections
SCOREBOX!
Outstanding performance in all areas addressed in this self-assessment may qualify you for recognition as an TOSHA approved Star Program participant.
Contacts |
---|
David BlessmanSTAR Program Manager |
Related Links |
---|
Volunteer STAR |